Sintered mesh filter cartridges, made from high-quality stainless steel wire cloth, provide precise filtration from 1 to 250 microns. They are widely used in industries such as pharmaceuticals, liquid and gas filtration, and fluidized bed applications. With excellent resistance to corrosion and the ability to withstand harsh operating conditions, sintered filters are an ideal solution for demanding filtration needs across various sectors.
Sintered Filters are advanced filtration products made from a combination of 5 or 6 layers of stainless steel wire mesh. These layers are bonded through a process of vacuum sintering, compression, and rolling, ensuring a durable and highly efficient filter.
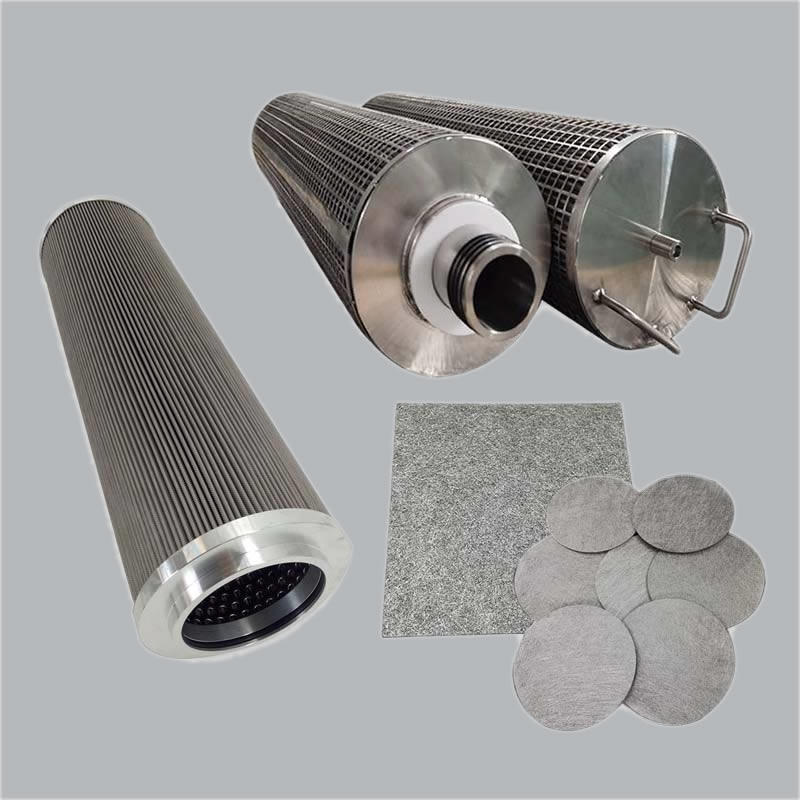
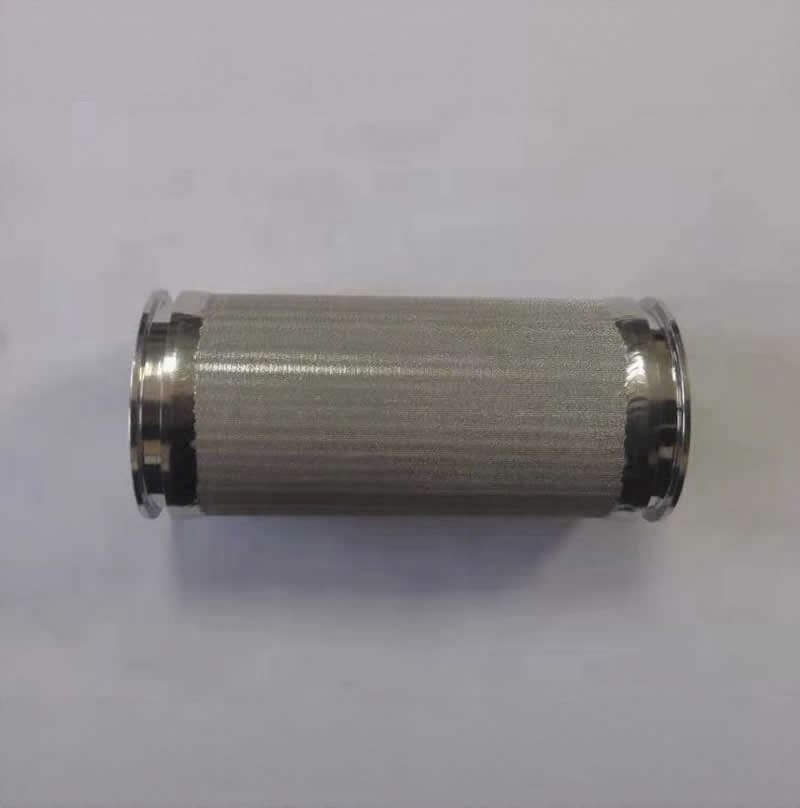
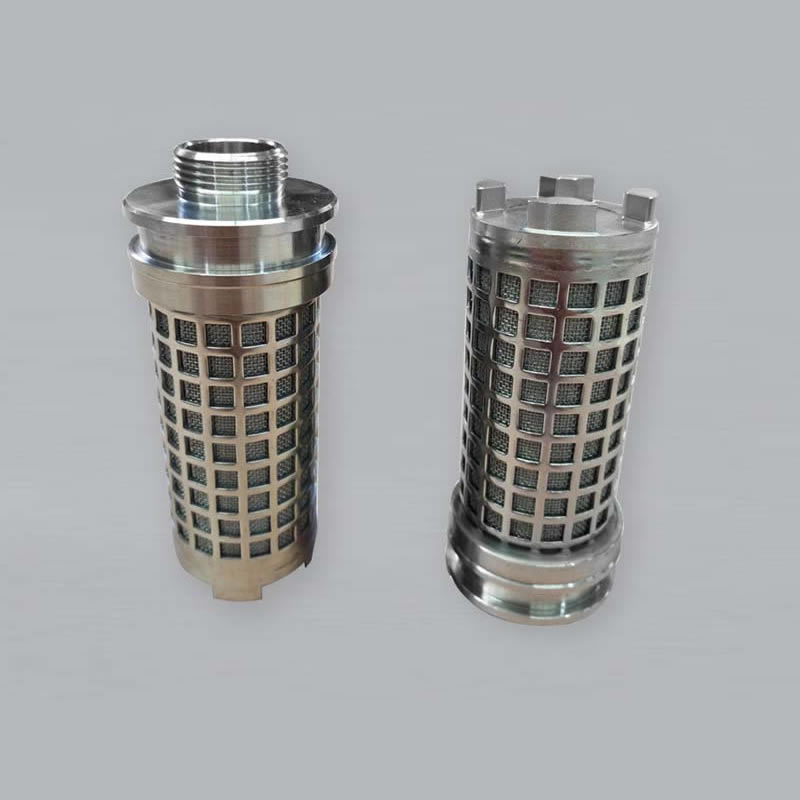
- 1st Layer: The protective layer, typically made from 100 mesh plain weave stainless steel wire mesh, safeguards the entire structure.
- 2nd Layer: The control layer, which can range from 150 to 450 mesh or include 165 x 600 to 400 x 2800 Dutch twill weave, offers precise filtration control.
- 3rd Layer: The dispersion layer, often made from 100 mesh plain weave mesh, evenly distributes the flow of fluid.
- 4th Layer: A reinforcing layer constructed from 12 x 64 mesh Dutch plain weave wire mesh provides structural strength.
- 5th Layer: The supporting layer, made from 64 x 12 mesh Dutch plain weave mesh, offers additional stability.
- 6th Layer (Optional): A second supporting layer of 12 mesh plain weave stainless steel wire mesh, included in some configurations for added strength.
Features
- Wide Filtration Range
Sintered filters offer a wide range of filtration ratings, from 1 to 100 microns, catering to various filtration needs. - Stable Filtration Performance
The protective and supporting layers ensure steady filtration throughout its use, even under tough conditions. - High Strength
Reinforced layers provide excellent resistance to pressure, making the filter ideal for high-pressure applications. - Easy to Clean
The surface filtration layer makes the filter easy to clean, especially from the reverse side, ensuring long-lasting performance. - Heat Resistance
It can withstand temperatures up to 500°C, making it suitable for high-temperature environments. - Corrosion Resistance
Made from stainless steel (304, 304L, 316, 316L), the filter resists corrosion in harsh environments. - Versatile and Customizable
Easily cut, bent, punched, or welded to meet various industrial requirements, offering flexibility in design.
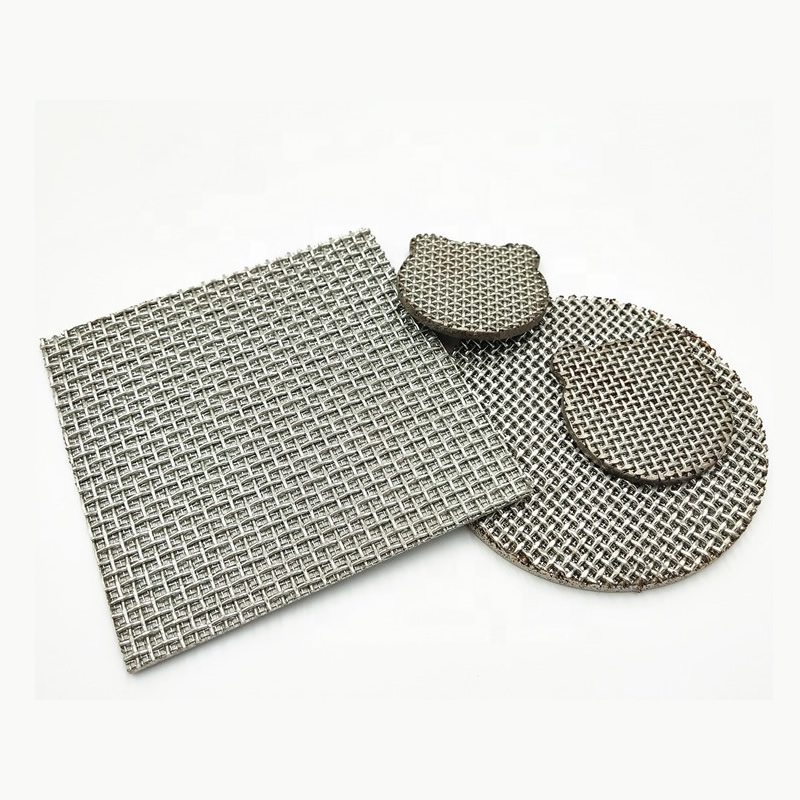
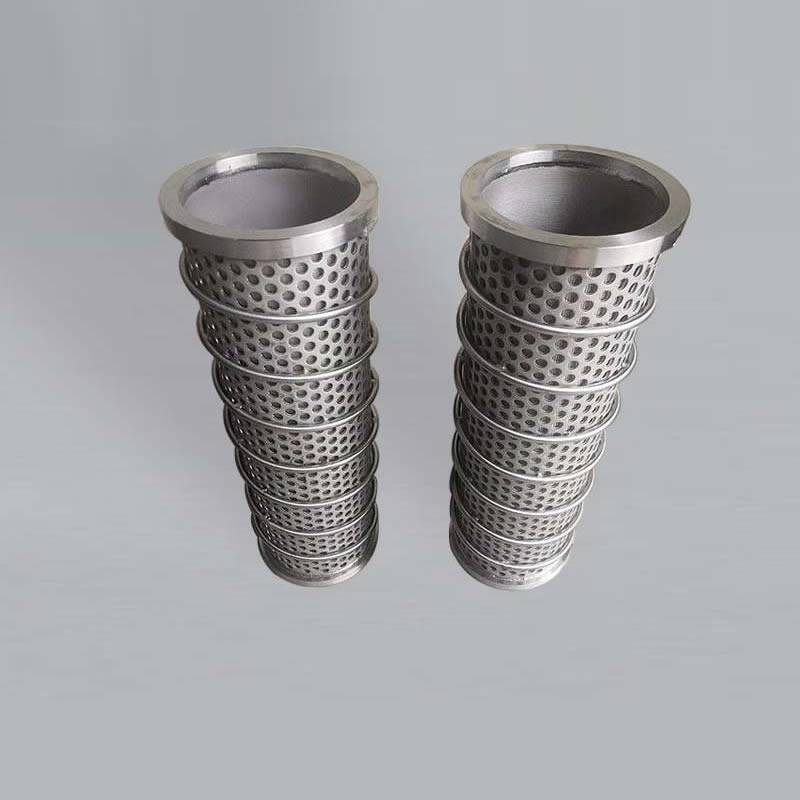
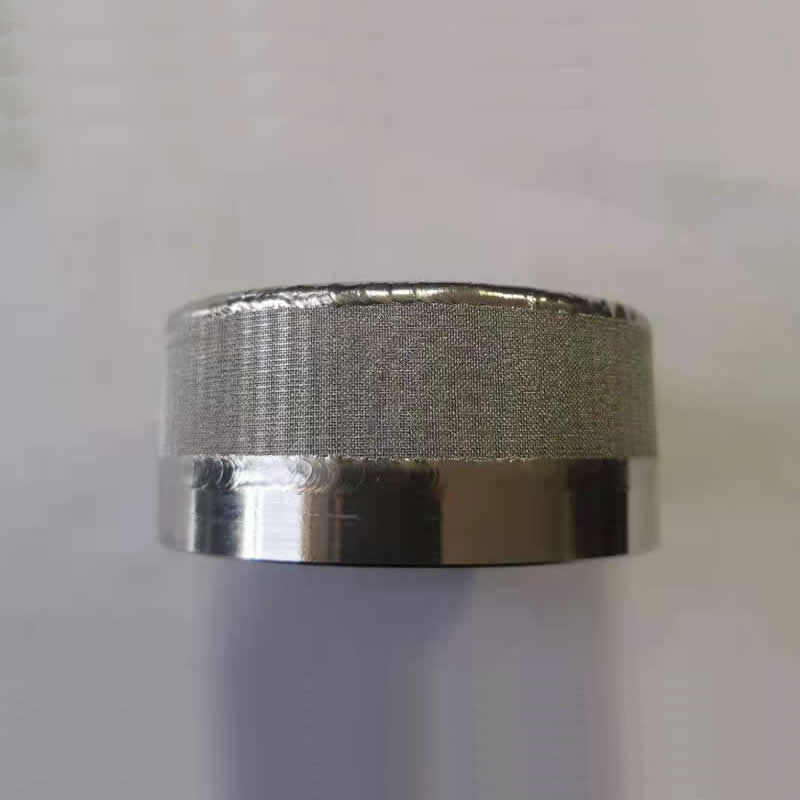
Applications
Sintered filters are widely used across various industries for their superior filtration capabilities.
- Pharmaceutical Industry
Used for filtration of drugs, ensuring the purity and quality of pharmaceutical products. - Fluidized Beds
Employed in fluidized bed systems for particle separation and uniform flow. - Liquid and Gas Filtration
Ideal for filtering liquids and gases in numerous industrial processes, ensuring clean and safe outputs. - Chemical Processing
Utilized for fine filtration in chemical production, improving product quality and process efficiency. - Chemical Fiber Filtration
Effective in the filtration of chemical fibers, helping to maintain high-quality production standards. - Food and Beverage
Used for food and beverage filtration, ensuring safety and clarity in liquids such as juices, wines, and oils. - Oil and Gas Filtration
Critical in the oil and gas industries for separating impurities and ensuring smooth operation of equipment. - Polyester Filtration
Applied in the polyester industry for filtering molten polyester, enhancing product purity. - Water Treatment
Essential in water treatment systems, removing contaminants to provide clean and safe water.
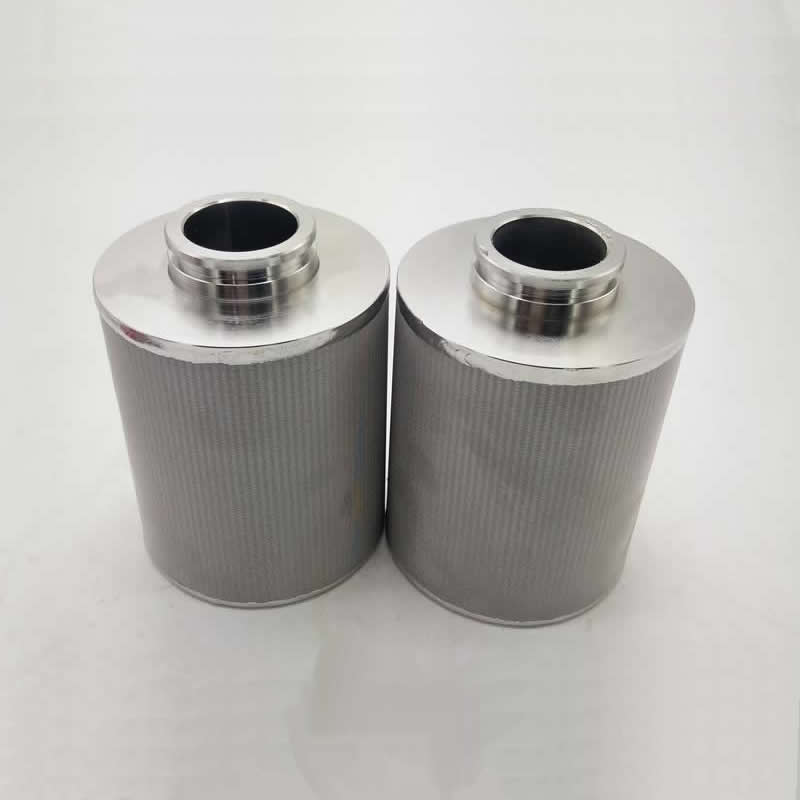
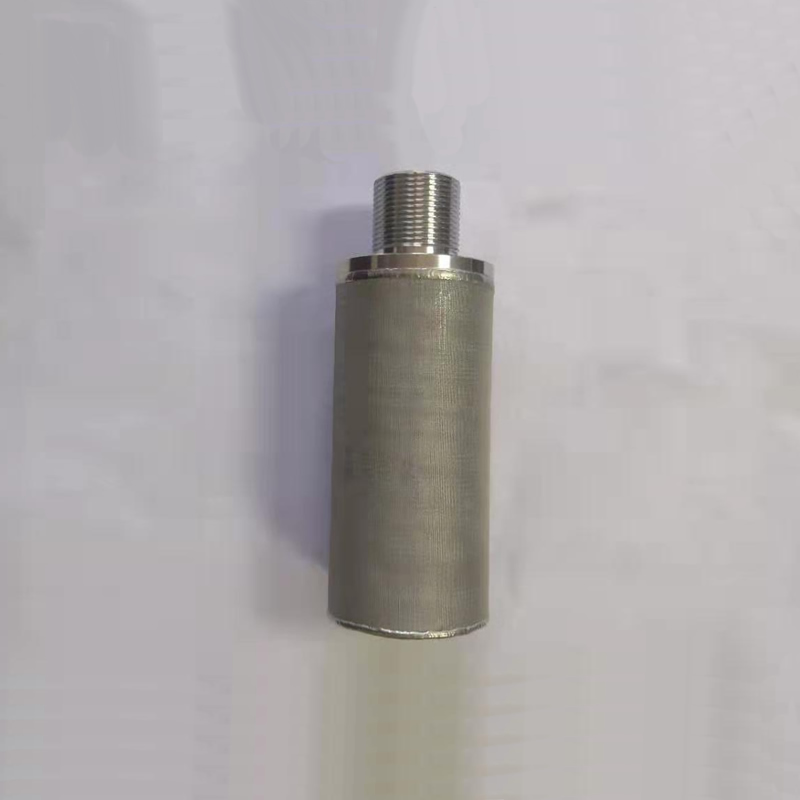
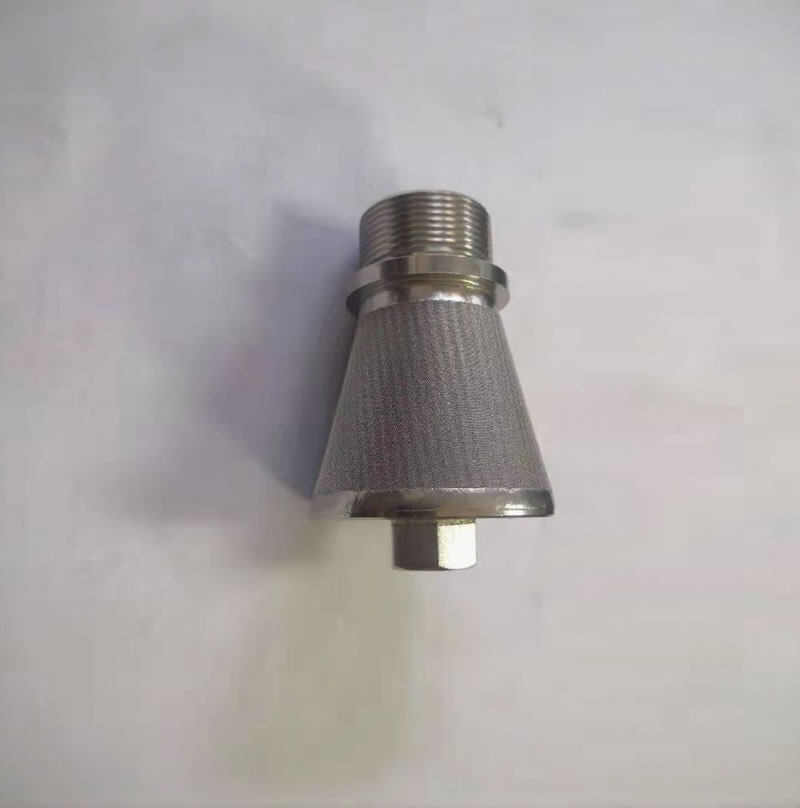
Specifications
Nominal Filter Rating (μm) | Protective Layer Mesh | Filtration Layer Mesh | Dispersion Layer Mesh | Reinforcing Layer Mesh | Reinforcing Layer Mesh | Thickness (mm) | Air Permeability (L/min/cm2) | Bubble Pressure (mm H2O) | Weight (kg/m2) | Porosity |
1 | 200 | 400 x 3000 | 200 | 12 x 64 | 64 X 12 | 1.7 | 1.81 | 360 – 360 | 5 Layers (8.4) 6 Layers (14.4) | Approx 40% |
2 | 100 | 325 x 2300 | 100 | 12 x 64 | 64 X 12 | 1.7 | 2.35 | 300-590 | ||
5 | 100 | 200 x 1400 | 100 | 12 x 64 | 64 X 12 | 1.7 | 2.42 | 260-550 | ||
10 | 100 | 165 x 1400 | 100 | 12 x 64 | 64 X 12 | 1.7 | 3.00 | 220-500 | ||
15 | 100 | 165 x 1200 | 100 | 12 x 64 | 64 X 12 | 1.7 | 3.41 | 200-480 | ||
20 | 100 | 165 x 800 | 100 | 12 x 64 | 64 X 12 | 1.7 | 4.50 | 170-450 | ||
25 | 100 | 165 x 600 | 100 | 12 x 64 | 64 X 12 | 1.7 | 6.12 | 150-410 | ||
30 | 100 | 400 | 100 | 12 x 64 | 64 X 12 | 1.7 | 6.86 | 120-390 | ||
40 | 100 | 325 | 100 | 12 x 64 | 64 X 12 | 1.7 | 7.10 | 100-350 | ||
50 | 100 | 250 | 100 | 12 x 64 | 64 X 12 | 1.7 | 8.41 | 90-300 | ||
75 | 100 | 200 | 100 | 12 x 64 | 64 X 12 | 1.7 | 8.70 | 80-250 | ||
100 | 100 | 150 | 100 | 12 x 64 | 64 X 12 | 1.7 | 9.10 | 70-190 | ||
150 | 50+100+50+30+30+100+50 | 2.0 | 25.00 | 50-150 | ||||||
200 | 40+80+40+20+40+80+40 | 2.0 | 26.00 | 50-150 |